|
Residual Stress
Conferences |
  |
M.B. Prime, T.J. Lienert, W.L. Stellwag, R.S. Casey, “Residual Stress Measurement in Friction Stir Welded Ti-6Al-4V,” Fabtech International and AWS Welding Show 2005, November 13–16, 2005, Chicago, Illinois. (LA-UR-05-8693)
Results:
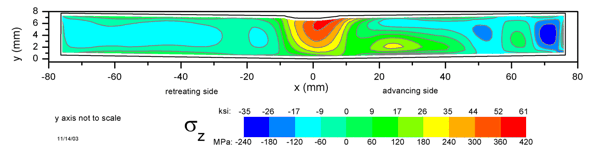
- Looks more like fusion welding stresses than the two peak distribution typical of FSW of aluminum alloys
- The stir zone or nugget exhibited residual tensile stress. A single peak of tensile stresses > 400 MPa was observed slightly below the surface corresponding to the shoulder of the tool.
- The stresses were asymmetric with higher stresses on the advancing side of the weld.
Friction Stir Welding:
- 0.285” thick Ti-6Al-4V plate - mill annealed
- FSW at 3.75 ipm and 275 RPM using inert gas box with sliding top.
- CP Tungsten tool with 0.75” diameter shoulder & 0.31” diameter pin (no threads). Cooled tool holder.
|
|
Macro metallography :
- Weld region displayed three microstructurally distinct zones
- Stir zone or nugget.
- HAZ (Heat-Affected Zone) or TMAZ (Thermo-Mechanically Affected Zone)
- Base metal
- Some Tungsten from tool observed
|
|
Microstructure:
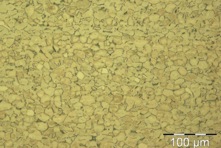
- Base metal
- Fine equiaxed grains of α
phase
- with small amounts of intergranular β phase
|
|
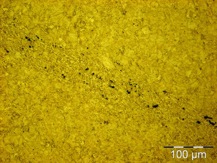
- Stir zone:
- GB α phase
- with fine
acicular α in prior β grains
|
Microhardness :
- 1 kg load & 15 seconds dwell
- Higher hardness in stir zone
|
|
Contour Experiment:
- Part was clamped in special fixture to minimize movement during cutting (see on picture on cutting page)
- Cut in wire EDM machine using 50 µm (0.002") diameter tungsten wire.
- Surface contour measured using laser scanner
- Peak-to-valley about 190 µm not including noise in data:
|
|
Calculate Stress using FEM
- Make 3-D model of plate after cut
- Start with flat surface
- Using displacement boundary conditions, force cut surface to opposite of measured contour
- Extract stresses normal to surface.
|
|
|
|